A compressed air audit is a thorough and complete evaluation of your system’s efficiency. While the heart of any compressed air system is its supply equipment: air compressors, filters, dryers, & receivers, the system also includes distribution piping header, sub-headers, point of use FRLs, and most important, your production equipment. During an audit, we asses all of these areas to determine where the inefficiencies and bottlenecks are.
An audit will take anywhere from a few days to over a week to complete. During that time, your compressed air system’s energy use is recorded and monitored to ensure we have a good baseline of energy required to support the current demand, as well as measuring pressures in different areas of the system to understand how the air is distributed throughout the system. In a lot of systems, flow measurement is required to understand of the true compressed air demand. In addition, dew point is taken so we know if we have a moisture contamination problem.
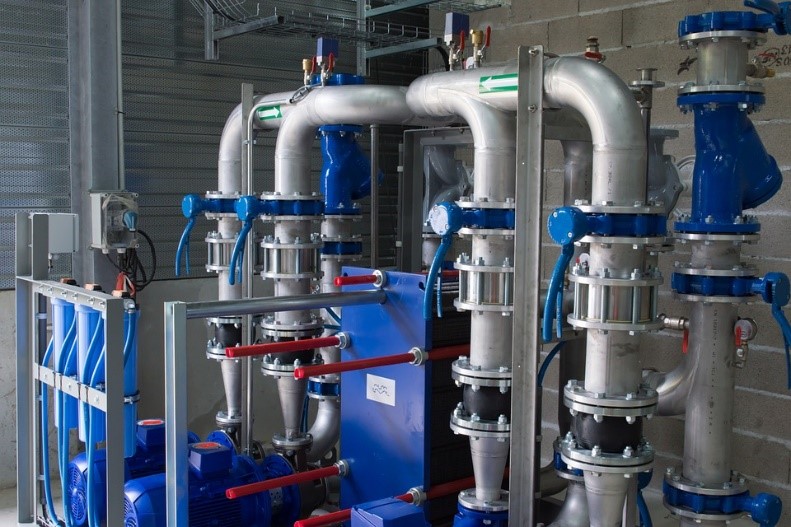
Industries that Benefit from Compressed Air Audits
A compressed air system audit is designed to optimize the system in conjunction with the company’s processes. Rather than just accounting for peak loads, an audit analyzes how a manufacturing facility is designed and how it operates throughout a timeframe. From this analysis, auditors suggest targeted improvement that can provide the most return on investment.
The goal is not to just update to the latest and greatest technology. Compressed air is used in a wide variety of industries including:
Paper Mills/Pulp Mills
Paper Converting
Printing/Envelopes
Plywood & OSM Mills
With such a broad range of applications, there is not a single solution that will work for everyone. A compressed air system audit is about identifying the solutions that fits a specific facility’s needs, budgets and goals.
How Compressed Air Audits Can Help Your Bottom Line
Ultimately, the real goal of a Case iZ compressed air system audit is to identify cost reductions and process improvements. Savings can be realized in the following ways:
- Performance Optimization – Reduce energy consumption through efficiency gains
- Equipment Longevity – Reduce maintenance cost & break fix repair cost on supply equipment
- Improvements and Enhancements – Reduce scrap rates and increase throughput & productivity
- Visualization – Provide continuous monitoring of KPIs so the above gains are maintained over a long period of time
A compressed air audit with Case iZ will result in a Project Proposal for a Turnkey Solution that will maximize energy savings, efficiency, and true system reliability.