A lesser-known element of compressed air systems is that their design profoundly impacts the reliability and productivity of their operation.
While the idea seems straightforward, there are many considerations that must be made early in the design phase; ideas that determine why an expert in compressed air system engineering is an invaluable part of your team.
At CASE iZ, we start with the basics and go forward from there.
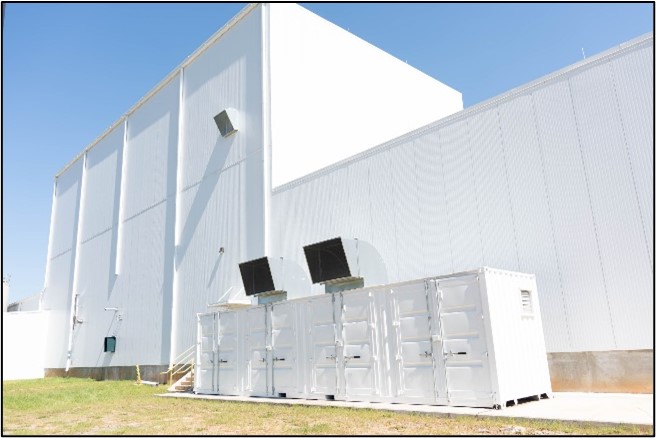
The first question a member of our team would ask you is: how will the air be used?
It seems like a simple question but a whole lot of the design concept behind optimizing your system hinges on the answer. A pharmaceutical manufacturing facility will have a very different system than an automobile plant!
Recognizing how your energy will be used dictates the type of compressors you’ll need – which inevitably will decide which type of technology of compressed air equipment you need and what type of system control and automation options we’d recommend.
So, the first step in intentional design is looking at:
(A) your application and processes
(B) the air requirement to operate that equipment and processes
The Logistics of Design
Once we’ve established the use of the air, we’d then consider some logistical components that will affect your air quality and reliability.
1. Power Sources
Industrial air compressors need access to three-phase power. To make installation and set-up easier (and cheaper), recognizing the ideal location of these power sources early in the design phase is essential.
Everyone wants to avoid getting to the point of installing the equipment only to discover that they need to run three phase power throughout an already existing plant.
2. Pipe Loops are crucial
The purpose of pipe loops is to decrease pressure drops between your system and your applications.
To put it simply, a loop is where your pipe splits from a header and “loops” around the perimeter of your facility, with other points of pipe connection included along the way to allow access to the application processes throughout a facility.
In larger systems, connecting the loop with cross pipe runs is a necessary design element to the piping system that will ensure the air flows efficiently throughout the system.
These steps cannot be overlooked when designing an efficient and sustainable compressed air system.
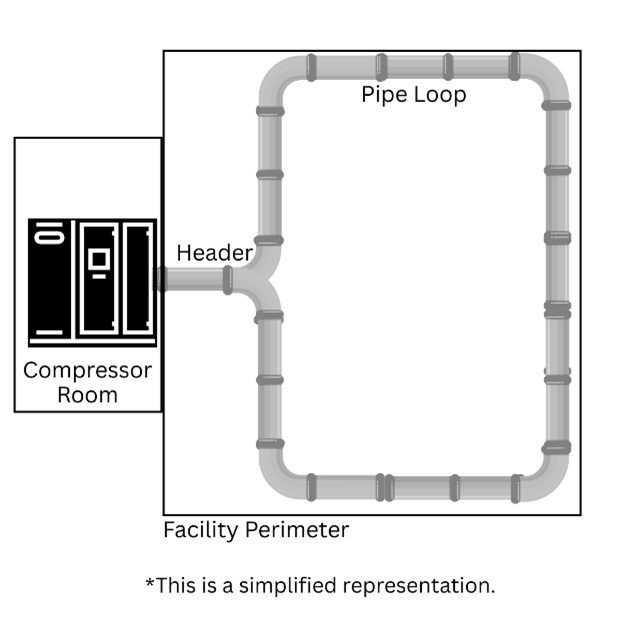
3. Environment Matters
The reliability of your air compressor can be manipulated by its environment.
If chemicals and various dust particulate can be ingested by your compressed air system, it will have negative consequences for your equipment over time. A protected and well-ventilated area without major temperature fluctuations is the most ideal place for your compressed air equipment to be housed.
4. Location, location!
A final piece to optimizing your system design has two parts of consideration;
A) The location of your compressed air equipment relative to your application; and
B) The location of your compressed air equipment in relation to one another
While some distances and configurations can be worked around or may be influenced by multiple buildings on one campus, the general considerations will be that you want your compressed air equipment closer to your applications and grouped together when possible.
System Automation
The best advice we can offer for saving money in the long run and increasing the reliability of your whole system is the inclusion of full system automation.
“Automation” seems to be a hot topic these days and there are many good reasons why. When it comes to your compressed air system, the list is long but we will include a few primary benefits below.
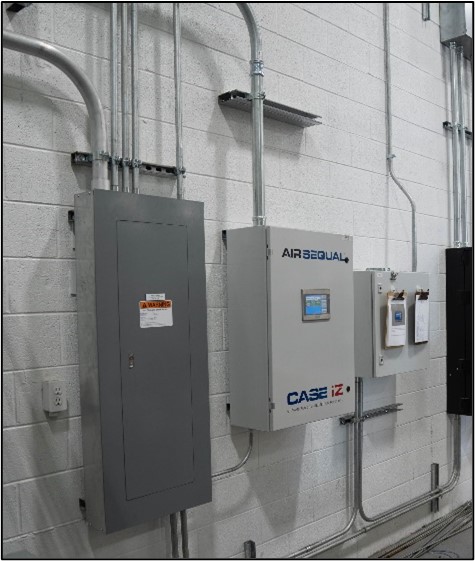
- System management that optimizes your energy
- Control of machines distributed around a plant from one master location
- Load sharing solutions that minimize energy waste
- Access to remote monitoring solutions like AirView Cloud
Summary
No matter the application of your compressed air, the intention behind the design will influence your success.
Application, power sources, pipe configuration, environment, system placement, and automation all impact the reliability and productivity of your equipment. This article has simply touched on some foundational design elements and did not even venture into specific types of equipment, accessories, and control options.
From this brief discussion alone, you can see the imperative nature of intentional design. At CASE iZ, we start with your production goals and use that information to build a system that will meet your standards and do it for a very long time.
Reach out to our team of expert engineers and find out what we can do for your facility!